COVER STORY, MARCH 2006
MIXED MESSAGES
Mixed-use developments meet rising costs.
Daniel Beaird
The continuing rise in the cost of building materials is the major trend that concerns the construction industry. However, developers and owners have pushed through these concerns by factoring it in their budgets, which has allowed the market to continue to grow. The popularity of mixed-use projects has spurred construction throughout the Southeast. The desire to move back into urban areas has sparked developers to turn to a live/work design.
With the popularity of mixed-use projects in urban areas, developers are having to search for undeveloped areas. When they can't find many, some are creatively remediating a city's brownfields for future development. Of course, this is a costly and timely process, but it has been proven successful with the development of Atlantic Station in Atlanta. As developers get used to the idea of building green and/or building LEED (Leadership in Energy and Environmental Design) projects, the governmental incentives for these programs are increasing. Hubert Construction is constructing Bowie Corporate Center in Bowie, Maryland. It is a LEED-certified office building that will save energy and improve worker productivity. “Three or 4 years ago, when you mentioned green, people thought you were talking about the color,” says Russ Gestl, executive vice president of Hubert Construction. “Now, nearly everyone asks if you had any experience with green.” And, the U.S. Green Building Council (USGBC) has done a great deal of work to streamline the LEED accreditation process. “I'm the first LEED-accredited professional in my company, and others have a strong interest in becoming accredited,” says David Gibbons, assistant vice president for SMCI in Washington, D.C.
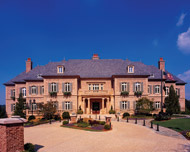 |
The Arthur M. Blank Family Office in Atlanta was the Southeast's first LEED gold-certified office building.
|
|
Atlanta-based Hardin Construction built the first LEED gold-certified office building in the Southeast with the construction of the Arthur M. Blank Family Office in Atlanta. It is home to the Arthur M. Blank Family Foundation and AMB Group. It is designed following the principles of the non-profit organization of minimizing environmental impact and perpetuating innovation in sustainability.
However, even with increased governmental incentives, LEED-certified projects remain costly, and with the current price of construction materials, those projects could be overlooked. Simple economics tells us that when demand exceeds supply, prices go up. In this case, way up. During one 6-month period in 2004 alone, steel rose 66 percent according to figures from the Associated General Contractors of America. The global economy has had a dramatic effect on these prices as China's burgeoning economy is in the process of building the Three Gorges Dam, a new highway infrastructure and eight new cities the size of Indianapolis. Here at home, building material prices began to rise when historically low interest rates met the rebuilding efforts from the hurricanes of 2004. Now, Hurricanes Katrina and Rita have effected the costs. “For a while, we were getting notifications of price escalations every week,” says J.J. McCarthy, president of Hubert Construction. “We are buying our materials as soon as possible and storing them to avoid more price escalations.” Bill Pinto, president and chief operating officer of Hardin Construction, believes it is flattening out. “We faced a very steep incline the past 2 years, but I think it will plateau. However, I don't see the cost and availability of materials dropping by any large extent,” Pinto says.
As developers search for ways to control their costs, processes like tilt-up construction have grown more interest. Tilt-up in-place material costs are more competitive than precast, masonry and steel structures. Fewer skilled laborers are needed for tilt-up construction, and the speed of construction and ease of other subcontractors' work reduce costs. “It's a higher quality product than it was 5 years ago,” Gestl says. “We are building a tilt-up with a cast in brick, and it looks like a brick in a precast office building.” Tilt-up projects do not require as much manpower, which benefits the industry since it is witnessing a shortage in skilled trades. “We are looking at anything that reduces the labor hours required to complete the job because you just can't find a good plumber or electrician anymore,” McCarthy says.
Processes like tilt-up projects all depend on the location of the building as well as the owner and developer. Washington, D.C.'s SMCI develops many office buildings for the federal government and certain security measures must be built-in after 9/11. “Because of public access, we have to build-in blast walls and other security measures,” Gibbons says. “These measures weren't seen before 9/11.” For example, the U.S. Defense Department had many of their employees located in offices in Arlington and Northern Virginia. These employees are being relocated due to those office buildings not being able to meet the new physical security requirements.
The construction industry is filled with many different trends to build on. Contractors continue to push through any concerns as the industry hit record high levels for construction last November. Last year's construction rate outpaced 2004's construction rate by 9 percent. However, developers and owners have to be wary of the price escalations within the industry. “We deal with the volatility of the marketplace every day,” Pinto says.
©2006 France Publications, Inc. Duplication
or reproduction of this article not permitted without authorization
from France Publications, Inc. For information on reprints
of this article contact Barbara
Sherer at (630) 554-6054.
|