Hampton Roads
Industrial Market
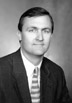 |
Phillips
|
|
In Hampton Roads, Virginia, current trends in the industrial
market include continued strong demand for owner-occupied
facilities due to low interest rates. Buyers continue
to seek 5,000- to 20,000-square-foot industrial buildings,
says Robert Phillips Jr., vice president of Thalhimer. While
Southside Hampton Roads will continue to experience a limited
supply of larger spaces, it appears that the Virginia Peninsula
may have a bit more than its share on hand with recent unrelated
plant closure announcements. Port-related uses will continue
to drive Hampton Roads bulk warehouse transactions.
The majority of industrial development is taking place in the
Southside Hampton Roads communities of Suffolk, Chesapeake and
Isle of Wight County, primarily because this is where the land
exists. This area also has a relatively low cost per acre and
higher concentration of labor. The more mature industrial submarkets
on the Virginia Peninsula, Newport News, Hampton and Williamsburg,
continue to offer select sites for development along major interstates
and arterials.
However, the concentration of new development will continue
at the edges of our market, Phillips adds. On the
west, the Greenmount Industrial Park, the location of a 2 million-square-foot
Wal-Mart distribution center, should see another distribution-related
announcement very soon.
Due to several plant closings, a large amount of inventory is
now available. These buildings include:
Federal Moguls 135,000-square-foot facility
in Hampton
John Deeres 307,784-square-foot manufacturing
facility in James City County
Gateway Computers 421,000-square-foot office,
manufacturing and warehouse facility in Hampton
Penn Engineerings 52,541-square-foot manufacturing
facility in Suffolk
Spiegel Groups 375,000-square-foot distribution
facility in Hampton
Two shell buildings: in Suffolk, a 50,000-square-foot
facility in Suffolk Industrial Park that is expandable to
130,000 square feet; in Franklin (Isle of Wight), a 58,000-square-foot
building in Pretlow Industrial Park.
On the positive side, examples of new construction/investment
include:
Target Stores development of its 1.5 million-square-foot
East Coast Import Distribution Center in Suffolk.
Sara Lee Coffee and Lipton Tea both significantly
expanded their plants and warehousing facilities in Suffolk.
The Newport News/Williamsburg Airport has announced its new
AirCommerce Park, targeting the air manufacturers and other
aerospace industry users requiring frontage on a concrete apron
(tarmac). While this manufacturing sector is notably down
at the moment, this development will broaden the future user/manufacturer
pool of new entrants to our marketplace, Phillips notes.
Another exciting and significant development that may result
in related industrial demand involves the National Institute
of Aerospace (NIA) and Craig Davis Properties development
of 60,000 square feet of office and research space in Hampton.
The NIA is a NASA-funded research center that may attract as
much as $400 million in grants over the next 20 years. NASA
Langley Research Center selected a six-university team headed
by the University of Virginia and Virginia Tech to direct the
development of technologies in aerospace and atmospheric science.
Construction is underway on this development, which is a tremendous
boon to the market and will positively affect the high-tech
segment of the Hampton Roads industrial market in the coming
years.
Absorption trends in Hampton Roads have been declining over
the past few years. According to the Old Dominion University
Center for Real Estate and Economic Developments 2002
Market Survey, Annual industrial absorption has continued
its downward trend from over 3 million square feet in 2000 to
approximately 2.8 million square feet in 2001 and now down to
approximately 2 million square feet in 2002. This drop in absorption
indicates an actual market growth of only 2 percent for the
year 2002. The stronger local absorption in the past 2 years
has been a direct result of large distribution facilities locating
in this market.
One notable concentration of absorption and investment occurred
in Chesapeake as a direct result of Fords 2001/02 Norfolk
Assembly Plant expansion to enhance the F-150 Truck production
and potentially the Super Duty F-series. TDS/US Inc. leased
450,000 square feet to sequence and meter parts for just-in-time
delivery to the Ford assembly line and Visteon leased 74,000
square feet to manufacture advanced plastic fuel tank systems.
The bulk of Hampton Roads inventory, like the nations,
screams for manufacturers. There are many outstanding manufacturing
properties available in Hampton Roads for all types of industry,
throughout the 35,000- to 90,000-square-foot range and above.
This existing product, the majority of which was built in the
mid- to late 1990s, can be found scattered between the westernmost
Williamsburg submarket and the Virginia Beach oceanfront to
the east. As Chesapeakes Winter 2002-2003 Economic Development
Report points out, Chesapeake and Hampton Roads are home to
several major automotive parts manufacturers, including Johnson
Controls, Nistem Corporation and Usui International, taking
advantage of existing building inventory, location, labor force
and pro-business climate.
The Hampton Roads industrial market snapshot is best captured
by Douglas Ellis, president of Ellis-Gibson Development Group
in Virginia Beach. Ellis has been involved in many notable industrial
projects throughout Hampton Roads over the years, including
the development of the 500,000-square-foot Cost Plus World Market
distribution center in Isle of Wight County.
We are a region of singles and doubles with regard to
normal industrial activity, Ellis says. Capital/business
investment is on hold, the demand side is very limited. Vacancy
rates/supply have been reasonable due to the realization by
most developers that our market does not justify large speculative
construction. Absorption has really been driven by distribution
centers for retail distribution, investment purchases for 1031
exchanges and local users purchasing older buildings capitalizing
on todays low finance rates. Public warehousers also play
a more active role due to their need for facilities inside which
to conduct their primary business. The above transactions, however,
should not be used to demonstrate health or normal business
demand or absorption.
I would add that this region remains as it always
has, ready and optimistic, says Phillips. We have
the location and infrastructure labor, ports, rail,
interstate, air, business climate, building and land inventory,
and incentives to both retain expanding companies and
attract new entrants. We are stable, stable, stable.
©2003 France Publications, Inc. Duplication
or reproduction of this article not permitted without authorization
from France Publications, Inc. For information on reprints
of this article contact Barbara
Sherer at (630) 554-6054.
|